工場のIoT活用は実装フェーズに入ったと言われるものの、いまだその手がかりを得られていない製造業は少なくない。IoT活用を本格化させるために、三菱電機は「東日本FAソリューションセンター」を2022年7月にリニューアルした。リニューアルのポイントは、顧客と議論しながら課題の発見と解決策の創出を目指す「共創型施設」への進化だ。実際どのように変わったのか、新しくなった同センターを訪問した。
IoT一辺倒だった次世代ものづくりのキーワードが変わってきている。展示会やセミナーのメインテーマに「IoT」が位置付けられることが、以前ほど見られなくなったのだ。
IoTに対する製造業の関心が薄れたわけではない。カーボンニュートラルなど製造業を取り巻く課題は多様化しており、課題解決の手段を求めるニーズはむしろ高まっているはずだ。関心が薄れたのではなく、IoTそのものに対する理解は業界に浸透し、製造業はそれを具体的に活用する次の実装フェーズに入ってきているからではないだろうか。それは「IoTとは何か」のような以前はよく見られたごく初歩的なプレゼンテーションが、今ではほとんど姿を消していることからも想像できる。
しかし現実に実装が進んでいるとは言いがたい。本格的に実装というステージに入るには、現場によってそれぞれ異なる課題を具体的に特定するという時間を要する作業が必要なためだ。当然ながら解決策の立案も個別対応にならざるを得ない。基礎的で一律な提案の意義が薄れた今、ソリューションベンダーはどのように製造業の関心をつなぎ止め、実装のステージに導こうとしているのか。逆に言えば、製造業は実装のステージに向かううえでどういう導き方をしてくれるベンダーに頼るべきなのか。
そんな環境変化の中、三菱電機の「東日本FAソリューションセンター」が、リニューアルにより実装のステージに向けた新たな提案を始めているという。さっそくどのようにリニューアルされたのかを見学してきた。
顧客と一緒に課題を「掘り起こす」
東日本FAソリューションセンターは2018年7月、東京・秋葉原に開設された施設だ。製造業のユーザ向けにFA機器を紹介・サポートする施設で、実際に機器を見て頂く「ショールーム(見る)」と、実機を試験頂く「テストエリア(試す)」、そして機器の基本性能や活用方法を学べる「トレーニングルーム:FATEC(学ぶ)」から構成される。2022年7月にショールームが4年ぶりにリニューアルし、単なる機器紹介にとどまらない施設に進化したという。
新しくなった東日本FAソリューションセンターは、「お客様との共創(Co-Innovation)の場となる課題解決型施設」というコンセプトを掲げている。そのコンセプトについて、リニューアルを企画したFAシステム事業本部の安部さんは次のように説明する。
FAシステム事業部 FAシステム業務部
デジタルマーケディングセンター
プロモーショングループ
安部潤一郎(あべ じゅんいちろう)
安部:従来の東日本FAソリューションセンターはロボットこそ業種別に展示していたものの、それ以外は機器を並べて展示したもので、一度見れば十分という印象の域を出ないショールームでした。機器を見てあとは営業の力量に任せていたのが実情だと思います。そこでデモ機を、具体的に何ができるのかといったソリューションを反映した内容に改善し、実際に動いているシステムを見てもらいながら、議論を通じて取り組むべき課題を浮き彫りにできる施設に作り替えたのです。
確かに表面的な課題とその解決方法が明白であれば、取り組むのはそれほど難しくない。しかし多くの場合、『真の課題』は現場からも管理者からも見えにくいところに潜んでおり、その存在すら気づかれないこともある。ならばそれを「掘り起こす」ところから支援していくことが、実装のステージに乗せるために必要な手段というわけだ。掘り起こすためには、製品を見せて後は顧客任せというわけにはいかない。「ソリューションを見せながら顧客と一緒に掘り起こす」という意志が、「お客様との共創(Co-Innovation)の場となる課題解決型施設」というコンセプトには込められている。
製品展示からソリューション展示へ。
さらにコミュニケーションに力を入れた
リニューアルされた施設内を安部さんに案内してもらった。入口を入って最初に目を引くのは「デジタルマニュファクチャリングエリア」にある模擬生産ラインだ。スマートウォッチの生産工程を模したラインで、ロボットによる文字盤のピッキングから取り付け、カメラによる画像検査、ロボットと人間の協働作業などを経て出荷に至るまでの流れを自動化した工程が再現されている。その中では機器の予防保全やAIによる省エネ支援がどのように行えるのかも示している。
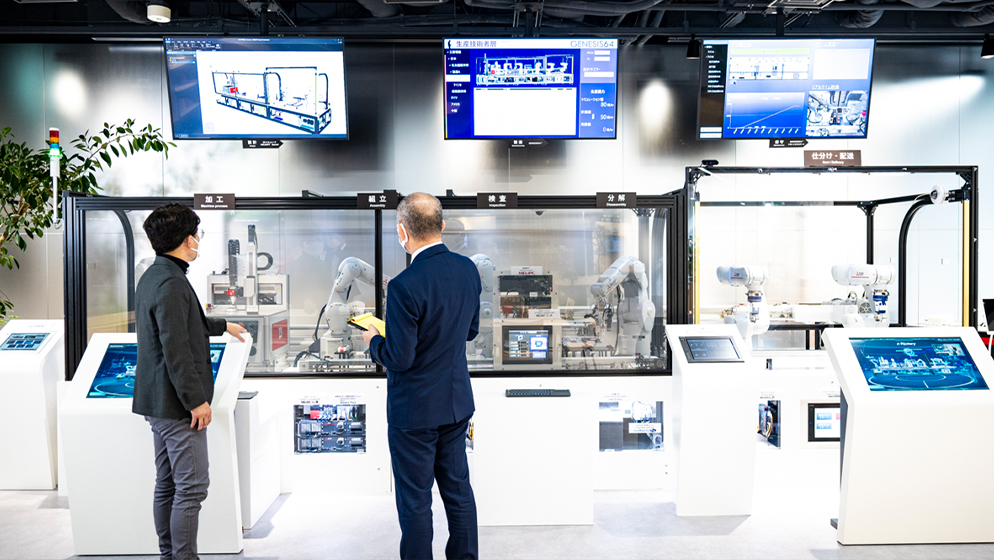
ラインの上にはモニタが3つ並んでおり、それぞれ3Dによるライン設計のシミュレータ、ライン全体の稼働監視、工場全体の監視の画面が映し出されている。シミュレータは生産ラインの設計検証をバーチャル環境上で行うもので、「デジタルツイン」を具現化したものだ。稼働監視のモニタではライン単位、工場単位で生産の実績を収集し、目標との乖離をリアルタイムで表示するなど、高度な生産管理を行う手法を紹介している。
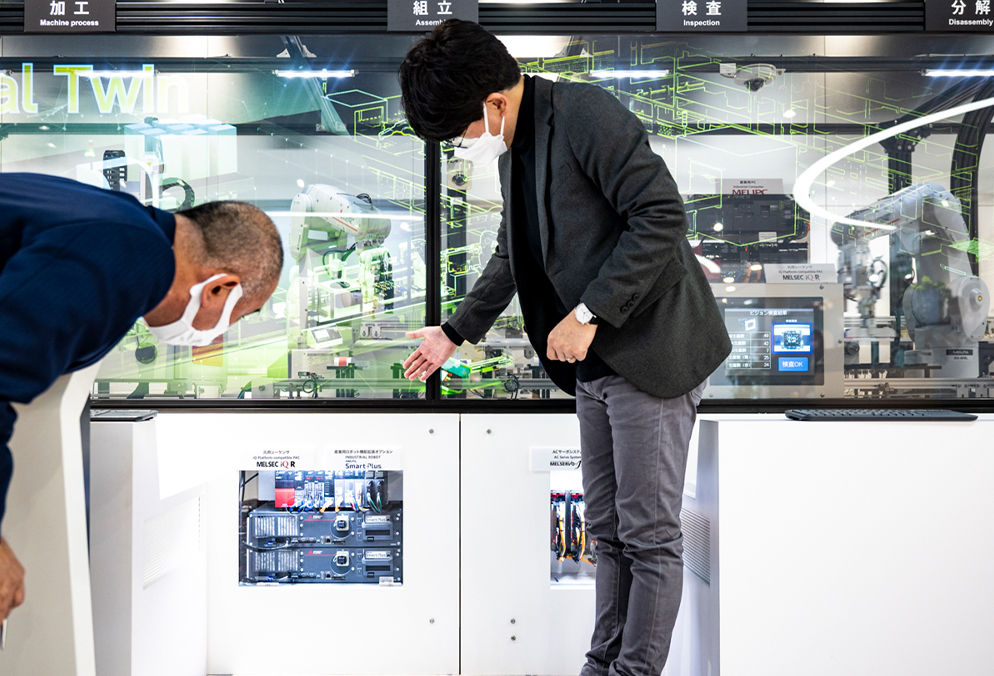
別のエリアには、実際にそうした高度なライン設計を実現するまでの流れを紹介する「装置設計シミュレーションドーム」がある。ここではハンドジェスチャーによる操作が実際に取り入れられていた。
シミュレーションドームでは、製造装置設計のシミュレーションからソフトウエアインストール、実稼働までの流れをハンドジェスチャーで操作できる
企画展示・セミナーなどが行われるイベントエリア。年に3~4回、さまざまな企画が実施される
その他、期間限定での企画展示やセミナーを行う「イベントエリア」や、ペンを持ったロボットが指定された文字や絵をガラス壁面に描くパフォーマンスが見られるゾーンもある。
これらさまざまなゾーンを見ていて不思議に感じたことがあった。一種のショールームにもかかわらず、ミーティングのための「コミュニティエリア」スペースが広くとられていることだ。
道沿いに設けられたショーウインドウには、ロボットが2台展示されている。端末で文字や絵、色を登録すると、両端に設置されたペンフォルダーからロボットがサインペンを抜き取り、ガラス壁面に登録された文字や絵を描いていく
安部:この施設は予約制ですが、予約段階で課題が明確なケースはほとんどなく、多くのお客様は現場改善のヒントが欲しくて悩んでいらっしゃいます。その漠然とした想いを抽出し、具体化するためのコミュニケーションに力を入れたフロア構成にしています。
IoTが何かという情報提供が十分行き届いた今、実装で効果を得るために求められているのは企業ごとに異なる課題の具体化であり、それを進めるには個々の企業に合わせた密な意見交換が必要だ。意見交換の場に重きを置き、展示物はその「火付け役」にすぎないというわけである。
安部:リアルのコミュニケーションだけでなく、海外や遠方のお客様とオンラインでつないだ意見交換や、当社FAの中核拠点である名古屋製作所の設計者も加えた技術打合せを行う事も考えています。加えて、イベントエリアをパートナー企業や代理店・特約店に開放し、ミニ展示会やセミナー会場として活用する事などもできるようになっております。
オンラインで撮影・配信可能な設備も導入しました。お客様・パートナー・代理店・特約店などあらゆる関係者を巻き込んだ、多様な「共創」ができるのではないかと思っています。
ベクトルを「課題解決型」に合わせる
バックヤードには課題具体化後の仕掛けも用意されている。課題の解決に使えそうな機器を実際にテストする「テストエリア」では、機器を使ってアイデアを検証することができる。センサだけでも多数のモデルが用意されており、いろいろ入れ替えながらテストが可能だ。IoTの実装過程では、初期段階でアイデアの実現可能性を確かめるPoC(概念検証)が重要となる。ただ、使える機器やサポートが限られているケースも多く、効果の検証が十分に行えないために経営層を説得できる材料が揃わず、アイデアがお蔵入りすることも多々ある。しかし東日本FAソリューションセンターのあるビルには、三菱電機の技術や営業の担当者が常駐するオフィスもある。使える機器が多く、すぐにサポートを受けられるここならば、PoCを納得いくまで進められそうだ。機器の活用方法を学べる「トレーニングルーム(FATEC)」も、別フロアに用意されている。
テストエリアでは、各種センサや接続機器を用意し、アイデアや機能などを検証することができる
安部:当社は、ここ数年、FAのソリューション部隊を再編制し、お客様への課題解決型の提案を強化してきましたが、ショールームは依然として製品を軸とした展示のままでした。これではお客様の課題に寄り添うことはできません。課題解決型にリニューアルされた東日本FAソリューションセンターでは、お客様と当社が、課題解決視点での “議論” “提案” を活性化させることができると考えています。
IoTの実装は、ものづくりのスマート化を進めていく中で製造業が乗り越えなければならない次のハードルである。そこには相当なパワーが求められている。しかし、お客様と三菱電機のベクトルを課題解決型で合わせる東日本FAソリューションセンターは、そのパワーを製造業に与えてくれる施設になりそうだ。
【東日本FAソリューションセンター】
- 所在地:東京都台東区台東1-30-7 秋葉原アイマークビル1階
- 開館時間:10:00~17:30
- 休館日:土曜日・日曜日・祝日・三菱電機の休業日
(その他、メンテナンスなどで休館となる場合があります)
- ※見学は事前予約制
- ※予約方法
下記公式ウェブサイトにある「ご予約はこちらから!」からお申し込みできます。
もしくは最寄りの支社またはお取引のある商社様にご相談ください。https://www.mitsubishielectric.co.jp/fa/jpsup/fas/east/index.html