「雪見だいふく」工場で進むスマート化、“完全自律運転” を目指すその第一歩
2020年4月 掲載
スマート工場化に積極的な取り組みを見せるロッテ浦和工場。モデルラインとして位置付ける「雪見だいふく」生産ラインでは「リアルタイム性」「エッジコンピューティング」をキーワードとし、設備の予兆保全と品質向上に取り組んでいる。同工場の取り組みを紹介する。
事例のポイント
- 1. 餅の仕上がりを左右するデータをEdgecrossで収集・分析
- 2. 餅ホッパーの振動分析で装置の予防保全を低コストで実現
- 3. 制御機器とのデータ連携によりライン全体を監視し、自動運転を目指す
株式会社ロッテ 浦和工場
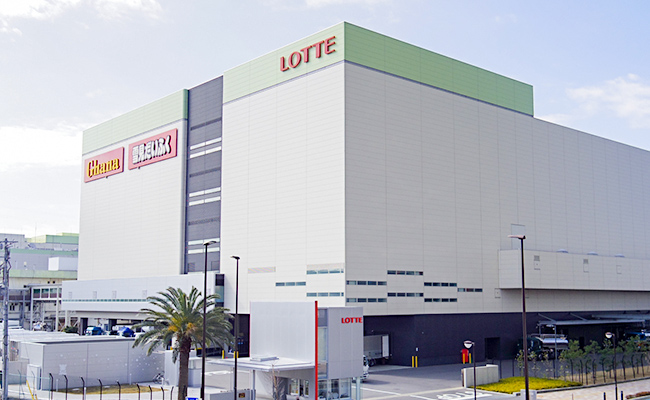
ロッテ浦和工場の外観 出典:ロッテ
衛生面や品質面など厳格な管理が求められる食品製造業。「プロセス製造」なども多く、自動化が進んでいる分野だが、実際には製造工程のさまざまな調整など、多くの工程が熟練技術者による “カン・コツ” で行われ、品質や生産効率を左右している状況である。しかし、人手不足や品質要求の厳格化、また食品ロスの低減などにより、製造現場での管理をより高度に行う必要が生まれてきている。これらを解決するために、IoT(モノのインターネット)やAI(人工知能)を活用したスマート工場化への関心が高まっている。
その中で積極的にスマート工場化を進めるのが、世界的菓子メーカーであるロッテの主力工場の1つである浦和工場だ。将来的には「“完全自律運転” を目指す」とする中、ロッテ浦和工場ではどのような取り組みを進めているのか。「リアルタイム性」と「エッジコンピューティング」をポイントに置き、スマート化で設備監視と品質向上を進める同工場の取り組みを紹介する。
「IoTやAIを使って工場で何かできないか」
1964年に開設されたロッテ浦和工場は、板チョコをはじめ人気商品である「パイの実」や「コアラのマーチ」「クランキー」などのチョコレート菓子や、「爽」「モナ王」「雪見だいふく」などの氷菓、アイスクリーム製品を製造する国内でも有数の生産規模をほこる菓子工場だ。ロッテには他に、狭山工場(埼玉県狭山市)、滋賀工場(滋賀県近江八幡市)、九州工場(福岡県筑後市)があるが、浦和工場は研究拠点としてのロッテ中央研究所も併設しており、操業当時から欧米の最新鋭機械を導入した主力工場として稼働してきた。
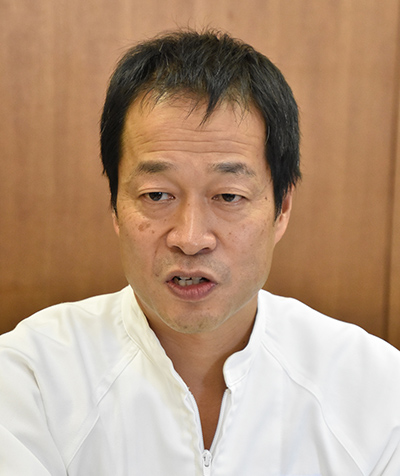
ロッテ浦和工場 施設部 部長の杉本浩氏
ロッテ浦和工場が、スマート工場化に取り組み始めたのは、もともと会社の上層部から「IoTやAIを使って工場で何かできないか」という指示があったからだという。生産性の改善に取り組むロッテ 浦和工場 施設部 部長の杉本浩氏は「人手不足や熟練技術者の引退など将来的な労働力不足などが見込まれる中でどうすべきかというのは、工場内でもさまざまな議論がありました。人手による対応に限界がある中で、技術で何とかしなければならないという点は漠然と考えていたところでした」と当時を振り返る。
実は、杉本氏はもともと浦和工場内でも “スマート工場化の原型” のような構想を描いており、さまざまな取り組みを進めていたという。「15年ほど前に研修で作成した資料でネットワークを構築して、全ての設備をつなげ、データを集めて分析する構想を示していました。当時から今でいうスマート工場のような姿が理想の工場の姿だと考えていました。」と杉本氏は語る。
その後、2010年頃には工場内で生産ライン更新の際に、生産ラインのトラブル、エラーの経歴、水や空気の使用量などのデータを収集し、生産の効率化に取り組んだこともあった。ただ、現場の設備担当者主導で実施し、運用の負担を軽減するような仕組みも導入できなかったことから、実際の運用がスムーズに進まず、一時的な改善はあったもののそれ以上の進展がなかったという。
当時は手軽に現場で負担なく使える技術が十分そろっていなかったということが推進の障壁となっていた。しかし、現在はAIやクラウドコンピューティング、エッジコンピューティングなどさまざまな技術が身近なものとなり、技術的にも費用的にも利用のハードルが下がってきている。そのため、上層部からのスマート工場化への指示は「チャンスだと考えました。思い描いていたことにあらためて挑戦できるとポジティブに捉えました」(杉本氏)とし、2017年から本格的に取り組みを開始したという。
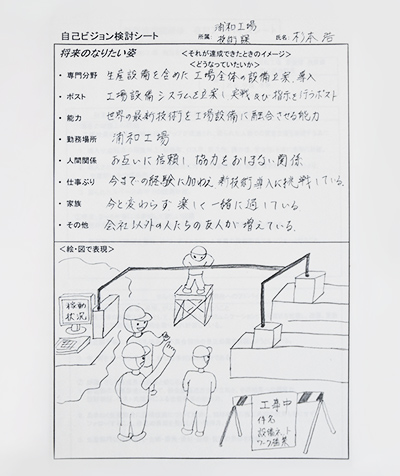
15年前に杉本氏が描いた理想の工場の姿。設備をネットワークでつなぎ、情報を収集するとともに、その情報を活用するというコンセプトが描かれている 出典:ロッテ
「リアルタイム性」と「エッジコンピューティング」がポイント
「スマート工場化の構想があった」といっても、実際に製造ラインに導入し、成果につなげていくのは簡単なことではない。まず、2017年の春から夏にかけて、事前準備として工場と本社との認識レベルの差を埋めるためプロジェクトチームを立ち上げた。その中で勉強会などを実施し、どういうことに取り組むのかを固めていったという。
一方で、制御機器やロボットなどのメーカーの訪問や、スマート工場に先行して取り組む企業の工場の視察などを重ね、自工場に採用できる技術などを模索していったという。ただ「プロセス製造でリアルタイムデータを活用したいという、われわれの描くものにぴったりはまるような技術や、それを採用している工場はあまりありませんでした。どういうものがよいのか試行錯誤が続きました」と杉本氏は語る。
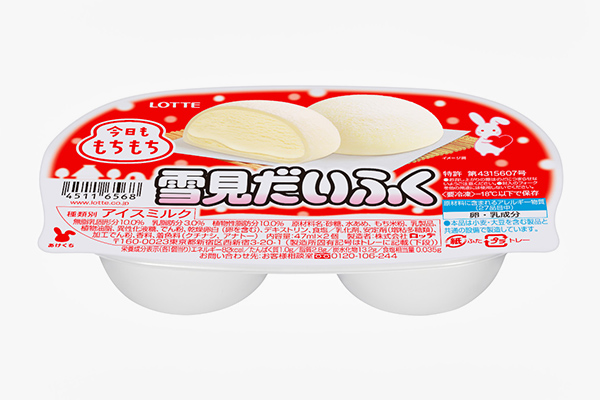
ロッテの主力製品の1つである「雪見だいふく」 出典:ロッテ
今回、ロッテ浦和工場で、スマート工場化のモデルラインに選んだのは「雪見だいふく」の生産ラインだ。「雪見だいふく」は1981年に発売したロッテの主力商品の1つである。アイスの外側を薄い求肥で包み、大福のように丸く整形した冷菓で、国民的アイスとして、爆発的な人気を誇っている。当初は「工程の構造がシンプルな『爽』のラインで導入することも検討していましたが、より複雑な工程を持つ『雪見だいふく』で行うことで知見や価値を生むことができると最終的に判断しました。他の工場への水平展開も視野に入れています」(杉本氏)。
取り組みのポイントは2つあった。1つは、原料などのバラつきに対応する機械の調整を従来は属人的な対応で行ってきたが、それをデータ化することで「品質の安定化」(不良品の抑制)を図るという点だ。そしてもう1つが、機械異常などによるライン停止を回避して素早くトラブル対応を行う「稼働率向上」を行う点である。
杉本氏は「IoTシステムの導入を検討する中で4つの条件がありました。1つ目は、ITとFAデータの連携(収集・整理)が容易にできるシステムであること、2つ目はリアルタイムデータ(特に瞬時データ)診断が可能なシステムであること、3つ目が、将来の機能向上や拡張性があること、4つ目が製造業への知見に基づいたデータの活用方法を一緒に構築できるベンダーが存在することです」と語る。
これらの条件の内でもいくつかは既に実現できている領域もあった。例えば、ITとFAデータの連携について、コンベヤーの制御にはインバータ、精密な作業の駆動部分にはサーボモータ、全体制御とデータ収集にはPLC、そしてそれらのデータを可視化するSCADAソフトウェアなど、三菱電機の製品を中心としてライン全体の稼働監視を実現していた。
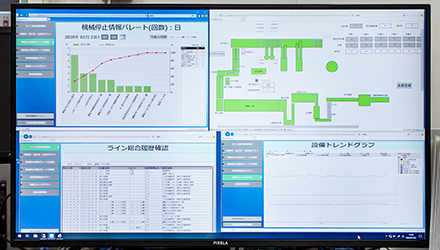
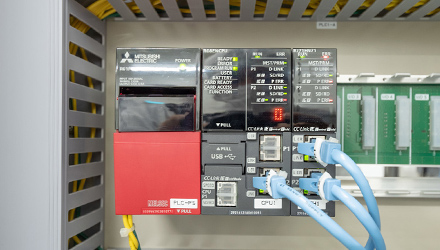
データの可視化をしているSCADA「MC Works 64」の画面(左)とデータの収集を担う「iQ-R」 出典:三菱電機
しかし、データを品質や稼働率向上に活用するためには「生産状況をリアルタイムに可視化する」ことが大きな壁となっていたという。「『良品をライン停止なく作り続ける』というのが目指す姿です。そのためには異常のデータを後で見直して改善するのではなく、ミリ秒レベルの瞬時データでリアルタイムに情報を取得して分析するということが欠かせませんでした。そのためには『クラウドに一度情報を送って分析する』というのでは不十分で、現場で情報を処理するエッジコンピューティングが欠かせませんでした。しかし、当時はなかなかこのコンセプトに見合う技術が存在しなかったのです」と杉本氏は当時を振り返る。
Edgecrossによる「リアルタイム」なデータ活用
技術を模索する中で、解決の糸口となったのが、2017年11月に開催された「システム コントロール フェア/計測展TOKYO(現IIFES、以下SCF2017)」だという。スマート工場化の実現に向けて情報収集に訪れた杉本氏が三菱電機ブースで見つけたのがEdgecross対応ソフトウェア「リアルタイムデータアナライザ」である。生産現場の予防保全、品質向上などを簡単に実現するデータ分析・診断ソフトウェアで、産業用PC「MELIPC」上で動作し、生産データのリアルタイム診断とオフライン分析を1つの製品で実現する。AI技術とさまざまな統計手法により生産現場のデータ活用を実現し、顧客の企業価値向上に貢献するなどの特徴を持つ。
「生産現場でリアルタイムに診断し即座に対応できる『リアルタイムデータアナライザ』をソフトウェアに持つ『Edgecross』は当社にとって最適な製造業向けオープンプラットフォームだと考えました。Edgecrossそのものもコンソーシアム形式で運営されており、ソフトウェアメーカーも含めて幅広い企業が参加しており、AIに関するアプリケーションをどんどん増やすこともできる可能性があるという点も魅力だと考えました」と杉本氏は語る。
当時はEdgecrossそのものが発表されたばかりで、対応製品はまだリリースされていなかったが、「すぐに導入したいと考えました」(杉本氏)とし、三菱電機に相談したという。ロッテ浦和工場では、それ以前にもPLCの9割を三菱電機の製品を採用するなど、制御関連で深い関係もあった。「三菱電機は常に新しい技術を提供してもらっており信頼感もありました。三菱電機からEdgecross対応ソフトウェアを導入するということは迷わず決めました」(杉本氏)としている。その後2018年春に本格的に導入を開始した。
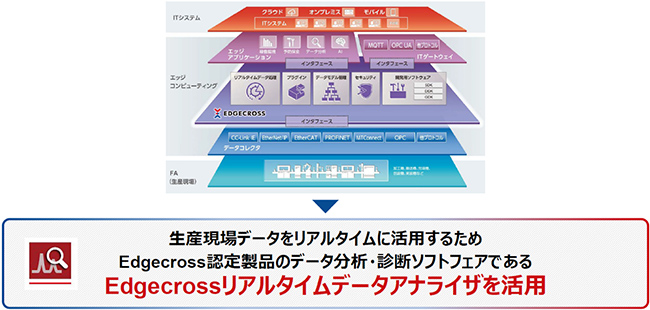
Edgecrossのコンセプトとリアルタイムデータアナライザの活用 出典:ロッテ
「雪見だいふく」生産ラインでの具体的な取り組み
今回、リアルタイムデータアナライザを導入した「雪見だいふく」の生産ラインだが、具体的な製造工程を見てみよう。雪見だいふくの生産工程は主に以下の6つの工程で行われている。
1. アイスミックスの混合、均質化
2. アイスミックス熟成
3. お餅蒸練
4. 包餡
5. 包装、急速冷凍
6. 梱包
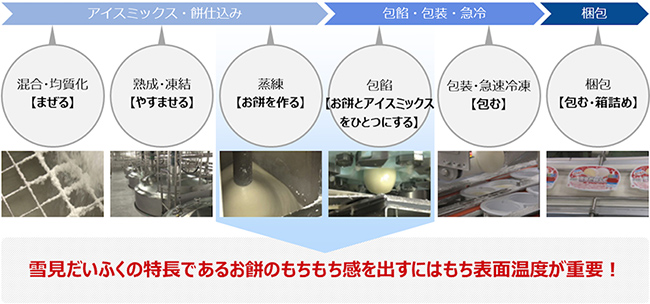
「雪見だいふく」の工程と、そのポイント 出典:ロッテ
この内、製品の品質安定化を図るために最も重要なポイントは餅の温度(温度が高いと餅は柔らかく、低いと硬くなる。餅に含まれる水分量に関係している)だという。それまでは現場熟練者の「カン・コツ」に頼っていた餅の仕上がり状態の把握を、システムの採用で、餅の仕込みから包餡工程に、温度をはじめ振動、圧力、電流などセンサを追加し、餅の仕上がりに関するあらゆるデータを「Edgecross」で収集することに取り組んでいる。
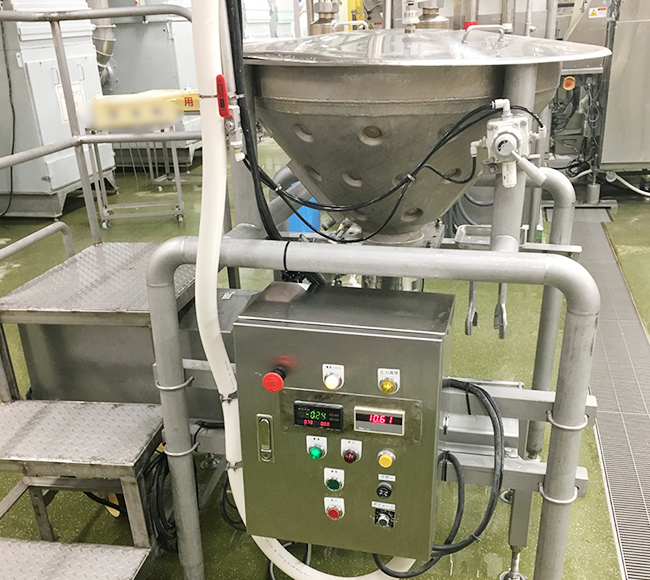
Edgecrossを通じてさまざまなセンサからの情報をリアルタイムで取得できるようにした餅ホッパー 出典:ロッテ
「AIを用いてさまざまな分析するために、計測項目を増やし、より細かいデータを出すことにこだわった。さらに、将来的に自律運転を目指すために、情報を出すだけでなく、書き込めるようにするための準備を整えた」(ロッテ 浦和工場 施設部 技術二課 課長の秋本浩史氏)とする。
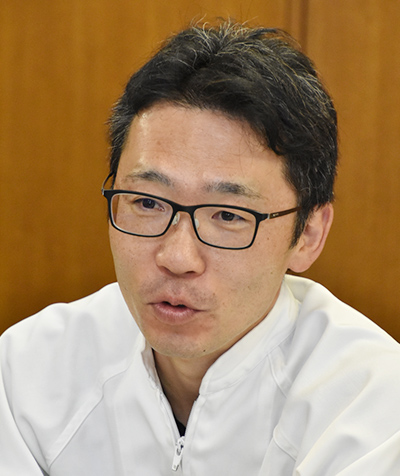
ロッテ 浦和工場 施設部 技術二課 課長の秋本浩史氏
具体的には、現在、オフライン分析として、分析ツールにより、餅温度、餅配管圧力、ポンプ電流値、振動値、などのデータから餅の仕上がりを左右する要因の分析を行い、餅の診断ルールを策定している。さらに、センサデータと正常パターンをAIが自動で分析し診断を行う。診断結果をリアルタイムに現場にフィードバックし、データに基づき対応することで、設備の自動調整を行うことも視野に入れているという。
現在は成果について確認しているところだが、既に「稼働状況と異常の関係や、想定していなかった箇所に異常があることなどが分かり、技術者のチームを作ってそれらを改善する取り組みも進めている」(秋本氏)など、さまざまな成果が表れているという。
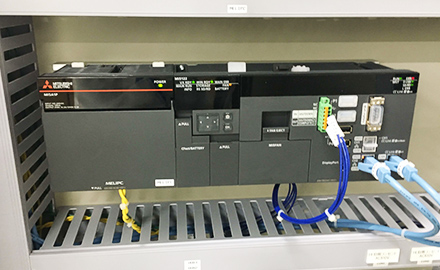
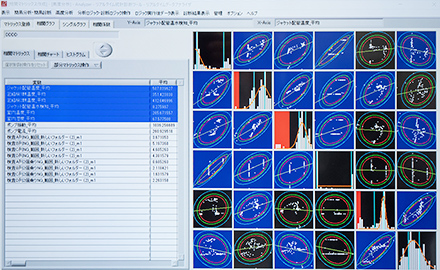
Edgecrossリアルタイムデータアナライザを搭載した三菱電機の産業用PC「MELIPC」と、相関分析画面 出典:ロッテ
また、現在取得しているデータ項目は、50カ所ほどに絞り込んでいるが、今後は「生産工程における時間の測定など、従来は取りたかったが取れなかった項目をさらに加えていきたい。データの収集については項目や粒度、精度などの面で充実させていく」(秋本氏)と、さらに詳細なデータ収集に取り組む方針だ。
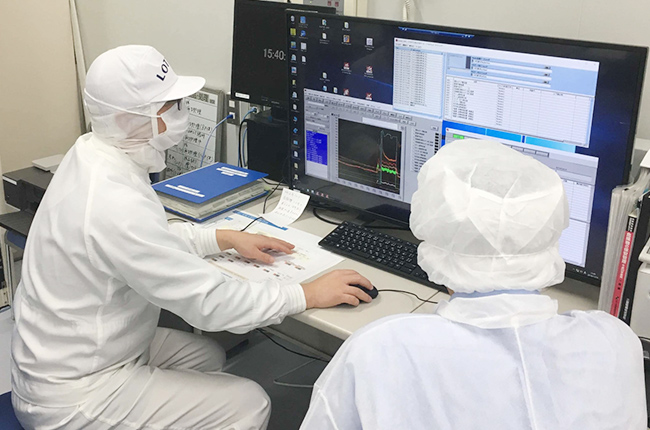
データを確認し改善に取り組む様子 出典:ロッテ
一方で、製品品質の安定化には装置の安定稼働も重要な要素となる。餅ホッパーなどの設備のチョコ停や故障は稼働率に大きな影響と損失を与える可能性がある。こうした予期せぬ故障に対しては、ホッパーのモータ部分に1ミリ秒単位でデータを取得できる振動センサを取り付け、分析と可視化を容易に行える「e-F@ctory支援モジュール」を使うことで、装置の振動解析と予防保全を低コストで実現している。
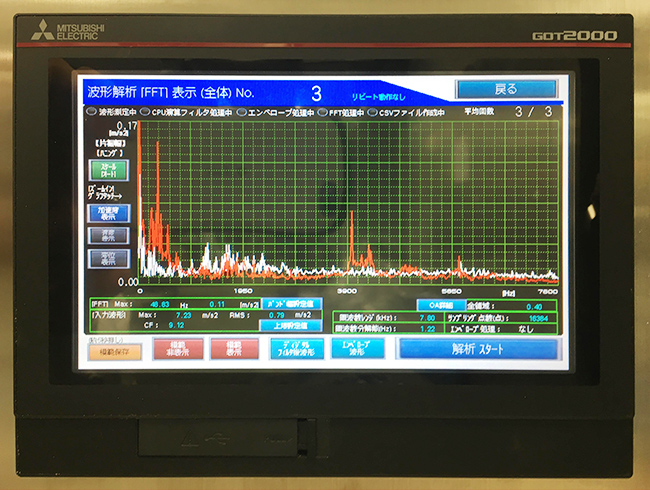
e-F@ctory支援モジュールの振動解析の様子 出典:三菱電機
工場の “完全自律運転” への道
また、システムを導入する上で協力会社の存在は大きい。今回、三菱電機のパートナーのナラサキ産業のマネージメントと三菱電機コントロールソフトウェアと日本電技のインテグレーションにより、きめ細やかなシステム要望に応えることができたという。
ロッテの浦和工場が将来的に目指しているのは “完全に自律的に動く工場” である。そのための前提として、SCADAシステムによるライン全体の情報収集などを基盤とし、これらの情報をさまざまな方向で活用していく方針だ。また、「e-F@ctory支援モジュール」などを生かして「見える化」による効果を創出しつつ、情報の取得箇所をさらに広げていく。
これらにより、「予知・予兆管理」機能を生かした「止まらないライン」「不良品を作らない、作れないライン」などを作り上げ、突発的な故障や連続不良のゼロ化を目指す。正常・異常の見える化による見回りなど作業負担の軽減や情報の共有化により改善のスピードアップにも取り組む計画だ。さらに、今回の「リアルタイムデータアナライザ」を用いた分析システムの導入は、今後、同じく雪見だいふくを生産している九州、滋賀の2工場への横展開なども行う。
杉本氏は「将来的には工場の “完全自律運転” が理想です。止める前、不良を出す前に、自律的に対応ができるような仕組みを作りたいと考えます。そのためにはさらにデータ項目が必要ですし、さまざまな検証が必要になります。近いステップとしてはリアルタイムの情報をフィードバックして部分的にも自動制御を行うということがありますがまだまだやるべきことがあります」と今後の取り組みについて語っている。ロッテ浦和工場の “完全自律運転” を目指す道のりは長いが、着実な一歩を刻んだといえるだろう。
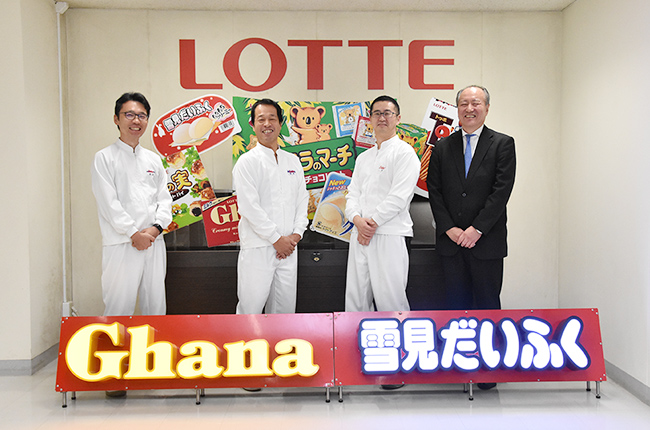
ロッテ浦和工場のスマート工場化に取り組むメンバー。左からロッテ浦和工場の秋本氏、杉本氏、卞氏、導入を支援したナラサキ産業の松永剛氏
転載元:MONOist
MONOist 2020年1月8日掲載記事より転載
https://monoist.atmarkit.co.jp/mn/articles/2001/08/news003.html
本記事はMONOistより許諾を得て掲載しています