金属3Dプリンタ(AM)
金属3Dプリンタとは? 方式、メリットを基礎から解説【動画あり】

三菱電機
金属3Dプリンタ(金属AM)
(AM: Additive Manufacturing)
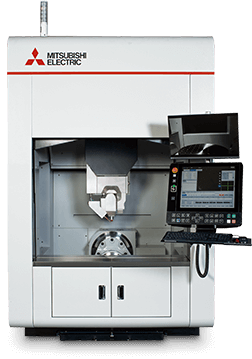
金属AMとも呼ばれている金属3Dプリンタの代表的な方式を画像や動画を用いながら分かりやすく解説。
三菱電機「ワイヤ・レーザ金属3Dプリンタ」の造形事例も掲載しています。
- 1.金属3Dプリンタ(金属AM)とは︖
- 2.金属3Dプリンタの種類と特長(主な方式)
- 3.【デポジション方式(DED方式)】三菱電機ワイヤ・レーザ金属3Dプリンタの特長
- 4.【デポジション方式(DED方式)】三菱電機ワイヤ・レーザ金属3Dプリンタの造形事例(適用事例)
- 5.受託造形サービスのご紹介
1.金属3Dプリンタ(金属AM)とは︖
金属3Dプリンタとは、ステンレス、チタンなどの金属材料をレーザや電子ビームなどで溶融、焼結させ、層を積み重ねていくことで目的の立体形状に造形していく装置のことを示します。プラスチックなどの樹脂を造形する「樹脂3Dプリンタ」もありますが、金属材料は樹脂と比べ大きなエネルギーを必要とし、熱影響も大きく安定造形が難しいなどの課題があります。
一方、昨今は金属3Dプリンタの造形精度・速度向上などの技術革新が顕著であり、従来では困難であった新たな製造方法やものづくりの実現のため、自動車、航空、発電、医療などあらゆる製造業において普及が始まっています。なお、金属3Dプリンタは金属積層造形、金属AM(Additive Manufacturing)とも言われています。
2.金属3Dプリンタの種類と特長(主な方式)
金属3Dプリンタにおける代表的な方式として、パウダーベッド方式(PBF方式)とデポジション方式(DED方式)があります。造形するための材料は金属粉末と溶接用ワイヤに大別され、溶融、焼結させる熱源としてはレーザ、電子ビーム、アークなどが用いられます。
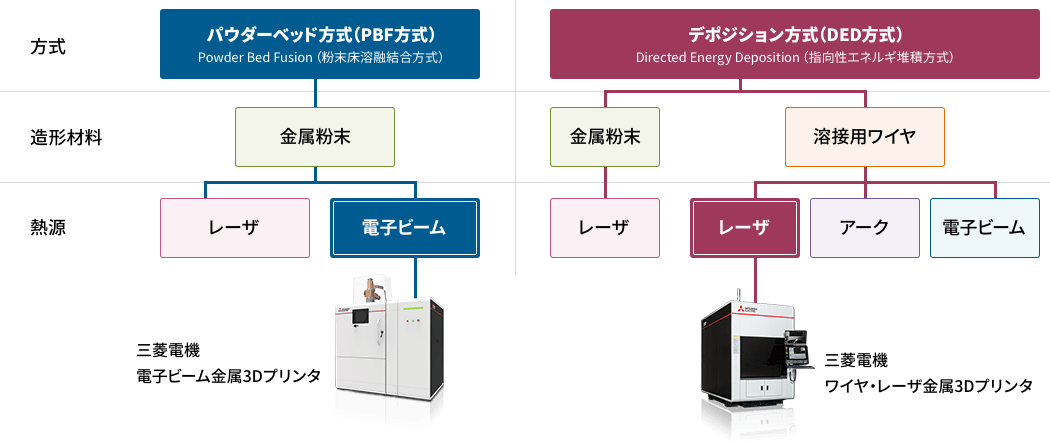
①パウダーベッド方式(PBF方式︓Powder Bed Fusion、粉末床溶融結合方式)
素材となる金属粉末を敷き詰め、造形する部分に熱エネルギー(電子ビーム、レーザなど)を照射し金属を溶かし固め、また粉末を敷き詰め溶融凝固と繰り返しながら一層ずつ積み上げていく造形方式。金属3Dプリンタにおいて、最も一般的な方式です。
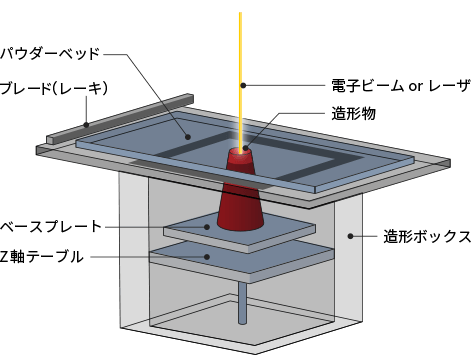
メリット
- 金型を必要とせず、ゼロから部品を製造することが可能である
- 従来工法では不可能であった複雑な形状生成が可能である
- 取り扱いメーカーが多岐に渡り、製品の選択肢が多い
デメリット
- 微細な金属粉末を用いるため、造形に時間を要する
- 部品設計を抜本から見直さないと効果が出にくい(DFAM※)
※Design of Additive Manufacturing(付加製造のための設計) - 金属粉末自体が高価であり、リサイクルやリユースが難しい
- 金属粉末同士を固めるプロセスのため
完成した造形物内に空孔が生じる場合がある - 金属粉末を取り扱うため、湿度の管理
粉塵爆発、健康被害への対策などが必要である - 造形後に溶融されなかった
周囲の金属粉末を取り除く手間が発生する - 造形物が崩れないように、サポート材*が必要な場合がある
サポートとは
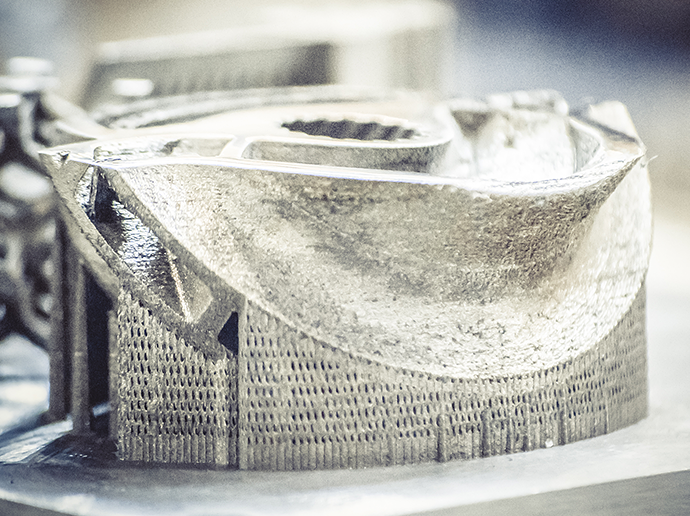
PBF方式の金属3Dプリンタは造形時に発生する熱の影響で造形物が収縮することがあるため、反り、寸法誤差などを最小限に抑えるためにサポートを付ける必要があります。
サポートを設けることへの課題としては以下があります。
- サポートを含めた造形設計検討の必要性
- 造形後のサポート除去工程の必要性
- サポート部にも造形コストが発生
②デポジション方式(DED方式︓Directed Energy Deposition、指向性エネルギ堆積方式)
基となる部品(基材・部材)に対し造形材料(金属粉末もしくは溶接用ワイヤ)を供給しながら、熱エネルギー(レーザ、電子ビーム、アークなど)を照射し、金属を溶かし固め堆積させて肉盛りするような造形方式です。
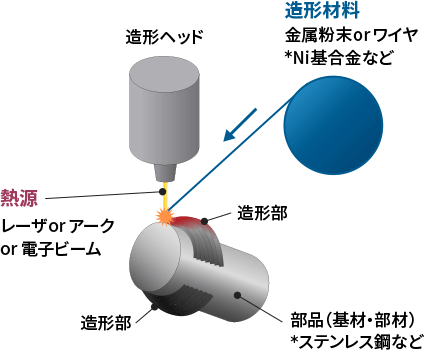
メリット
- 造形が速く、大型部品の造形にも向いている
- 必要な箇所に付加造形が可能なため、金型/部品補修や
異種金属造形が可能である(部品の高機能化) - 部品設計を抜本から見直さなくても効果が出しやすい
デメリット
- 複雑な形状の造形には不向きである
(造形形状には制限がある) - パウダーベッド方式に対し、造形精度が劣る
②-1 パウダー×デポジション方式(DED方式)
金属粉末を吹きかけながら、レーザなどの熱エネルギーを照射して基となる部品(基材・部材)に金属粉末を溶融、堆積していく方式。熱源がレーザの場合は金属粉末が酸化を防ぐため、アルゴンガス(Ar)などの不活性化ガスを装置の造形エリア内に充満させて、造形を行うのが一般的です。基となる部品に薄い被膜のような追加造形や、異なる金属粉末を混ぜながら造形材料を供給することも可能です。
メリット
- 基となる部品に薄く被膜のように付加造形が可能である
- 異なる金属粉末を混ぜながら供給することも可能である
デメリット
- 微細な金属粉末を用いるため、造形が比較的遅い
- 金属粉末を吹きかけながら積層するため、一部は溶融されず
飛散するなど歩留まりが悪い(造形寄与率は60%※程度)
※メーカー、造形形状などにより異なる - 金属粉末自体が高価であり、リサイクルやリユースが難しい
- 金属粉末同士を固めるプロセスのため
完成した造形物内に空孔が生じる場合がある - 金属粉末を取り扱うため、湿度の管理
粉塵爆発、健康被害への対策などが必要である
②-2 ワイヤ×デポジション方式(DED方式)
熱エネルギー(レーザ、電子ビーム、アークなど)を照射して基となる部品(基材・部材)に溶接用ワイヤを溶融、堆積していく方式です。造形が速く、大型部品の造形に向いており、一般市販の溶接用ワイヤを使用するため廉価です。また、爆発や健康被害の懸念がなく、安全で管理が容易です。高い構造強度と耐久性をもつ造形が可能であり、完成した造形物内に空孔が生じにくいといった特長もあります。
メリット
- 溶接用ワイヤを溶融凝固させるため、造形が速く
大型部品の造形にも向いている - 造形材料が一般市販の溶接用ワイヤにつき安価である
- 供給したワイヤのほとんどが積層されるため、歩留まりが高い(造形寄与率は95%※以上)
※メーカー、造形形状などにより異なる - 溶接用ワイヤにつき、金属粉末に比べ湿度管理が容易で
爆発や健康被害の懸念が無く、安全で管理が容易である - 高い構造強度と耐久性をもつ造形が可能であり
完成した造形物内に空孔が生じにくい
デメリット
- 造形精度、面粗さが高くないため
後工程(機械加工による仕上げ)が必要である - ワイヤを安定送給しながら造形することが技術的に難しい
- 造形時の熱影響による積層ズレなどが発生しないよう
造形することが技術的に難しい
3.【デポジション方式(DED方式)】三菱電機ワイヤ・レーザ金属3Dプリンタの特長
デポジション方式(DED方式)、供給材料に溶接用ワイヤ、熱源にレーザ(ファイバレーザ)を採用した三菱電機ワイヤ・レーザ金属3Dプリンタ「AZ600」を2022年3月に発売開始しました。
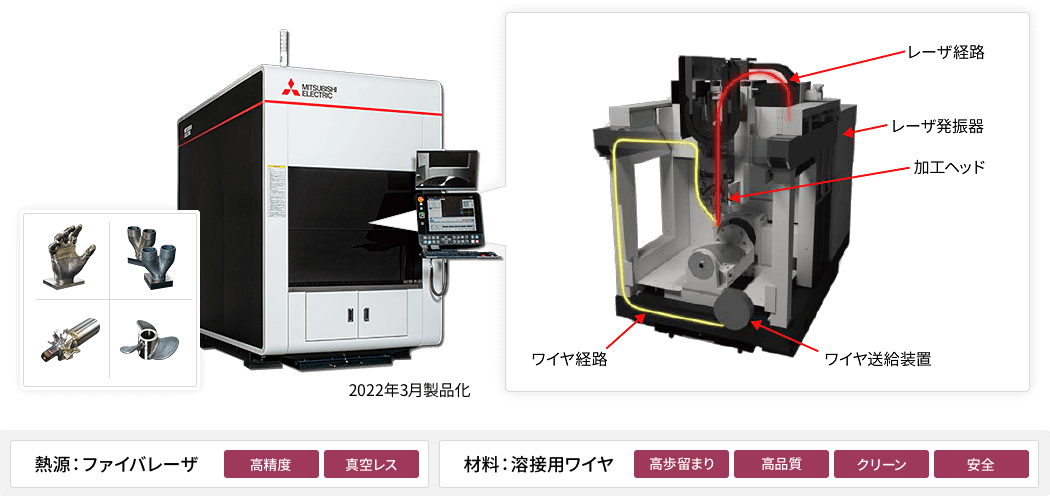
長年培った自社技術、自社キーコンポ―ネントを結集し、空孔のない安定した造形を実現します。
- ワイヤ放電加工機 → ワイヤ送給技術
- 板金レーザ加工機 → レーザ出力制御技術
- 数値制御装置(CNC) → 協調制御技術(5軸制御×ワイヤ送給制御×レーザ出力制御)
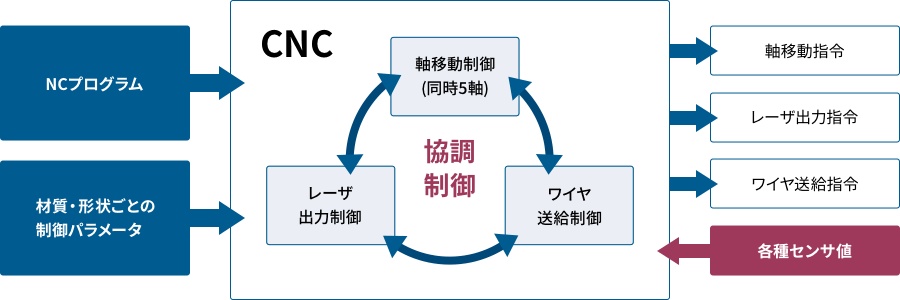
緻密な積層造形
独自の造形プロセス制御技術により、積層ずれ、だれなどを抑制。
造形状態を常に計測し、ワイヤ送給速度、レーザ出力、軸移動を自動でコントロールします。
造形状態に応じて自動調整
加工面の形状に倣いながら造形
加工面の凹凸が平坦となるように造形
センシング、溶融モニタリングにより、造形状態に合わせて、①ワイヤ送給速度、②レーザ出力、③軸移動を自動調整。独自の造形プロセス制御により、造形破綻、空孔のない安定した造形を実現します。
4.【デポジション方式(DED方式)】三菱電機ワイヤ・レーザ金属3Dプリンタの造形事例(適用事例)
①ニアネットシェイプ工法
従来工法では切削のみで部品を製造していたのに対し、基となる部品(基材・部材)に必要な箇所のみ造形し後加工(切削)することで、加工時間、材料廃棄量、製造コストを削減する工法です。
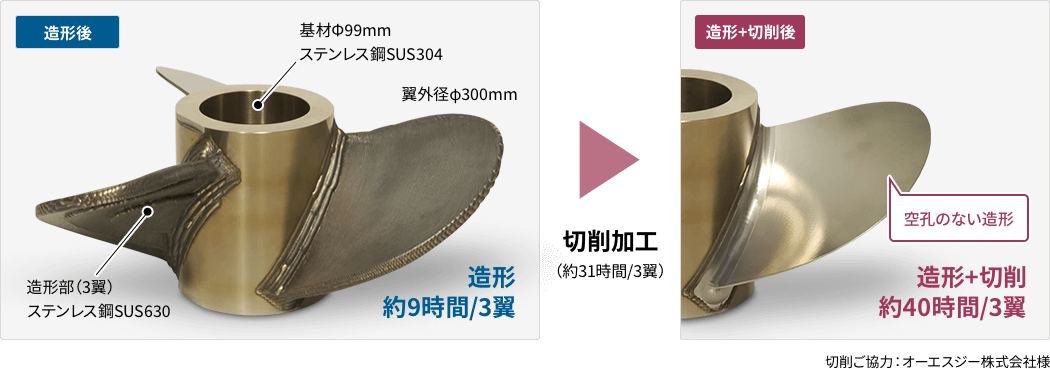
ニアネットシェイプ方式を取り入れ、従来工法に比べて大きく効率化することが可能です。
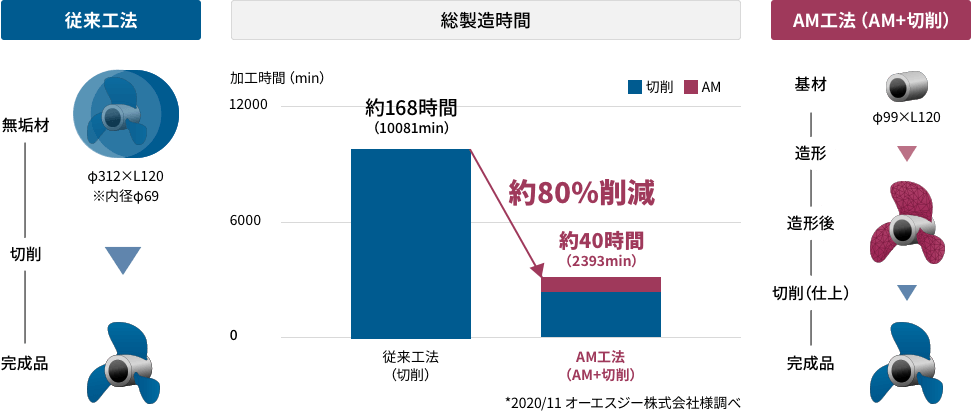
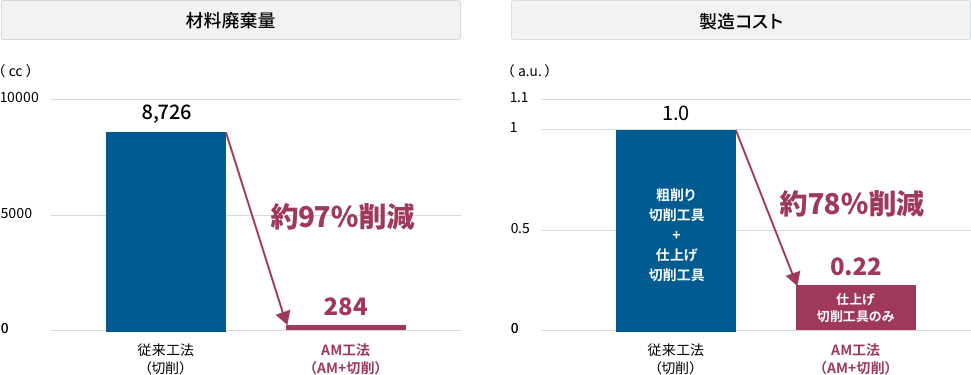
②溶接代替(部品溶接自動化)
従来のTIG溶接(熟練工による手作業)を金属3Dプリンタに置き換えることで手作業によるばらつきを抑え、品質の安定・高速・省人化を図る工法です。センシング、溶融モニタリングによる自動調整が可能なため、溶接用ロボットでは難しい溶接にも対応します。また一部は溶接、一部は造形など一台二役を担うこともできます。
ステンレス鋼への開先溶接事例
- ■基材:ステンレス鋼SUS304
- ■造形材料:ステンレス鋼SUS308L
- ■造形時間:10 min(ビード17層)
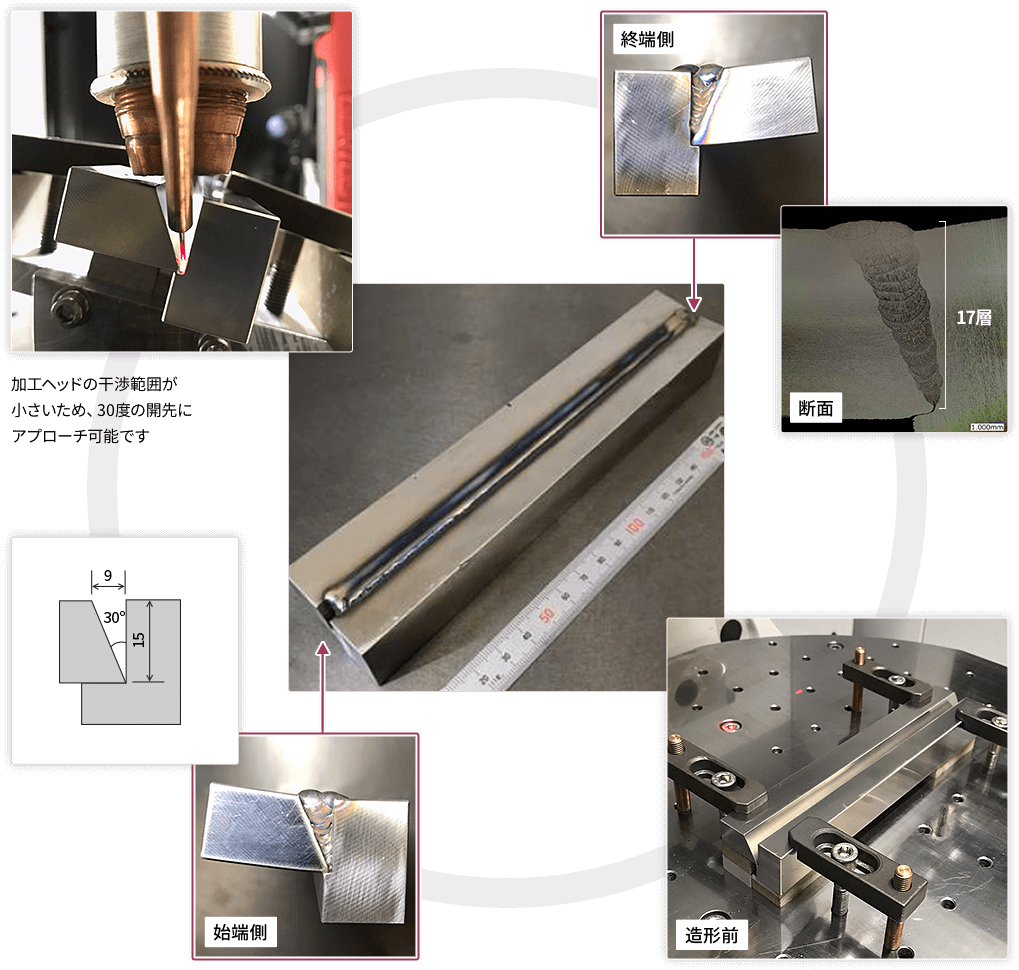
③金型補修
使用回数限度を超えダメージを受けた金型を、造形によって補修する工法です。従来のTIG溶接(熟練工による手作業)補修に対し、ばらつきの少ない高品質な補修かつ作業時間の短縮が可能です。
従来
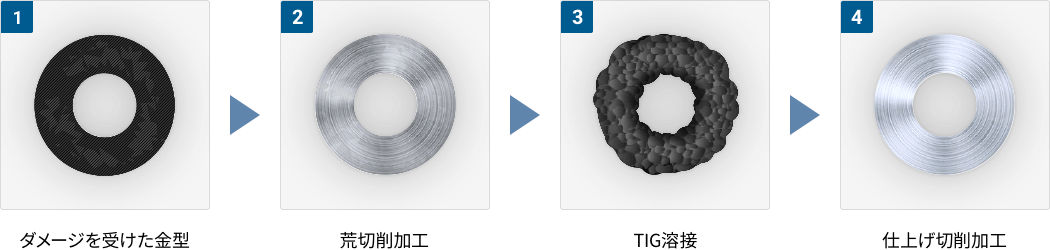
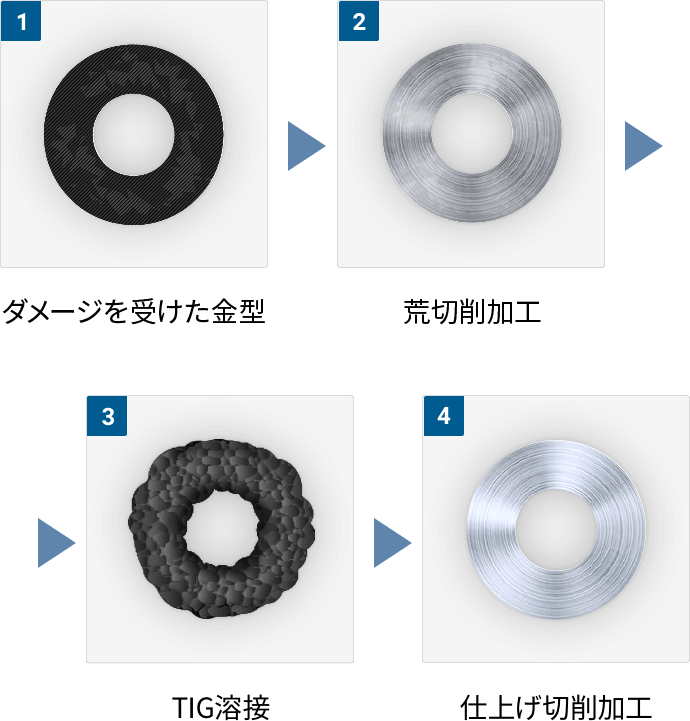
金属3Dプリンタ
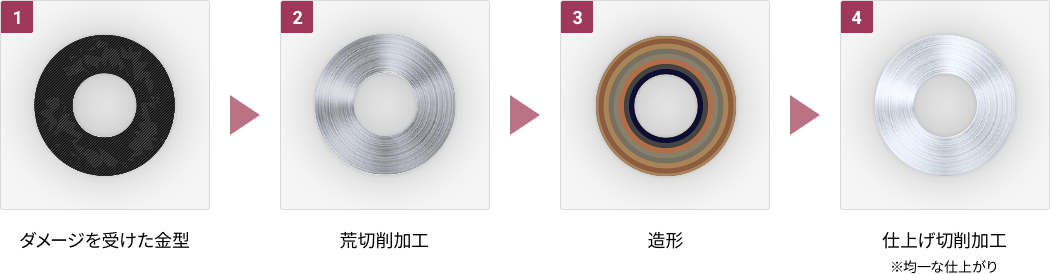
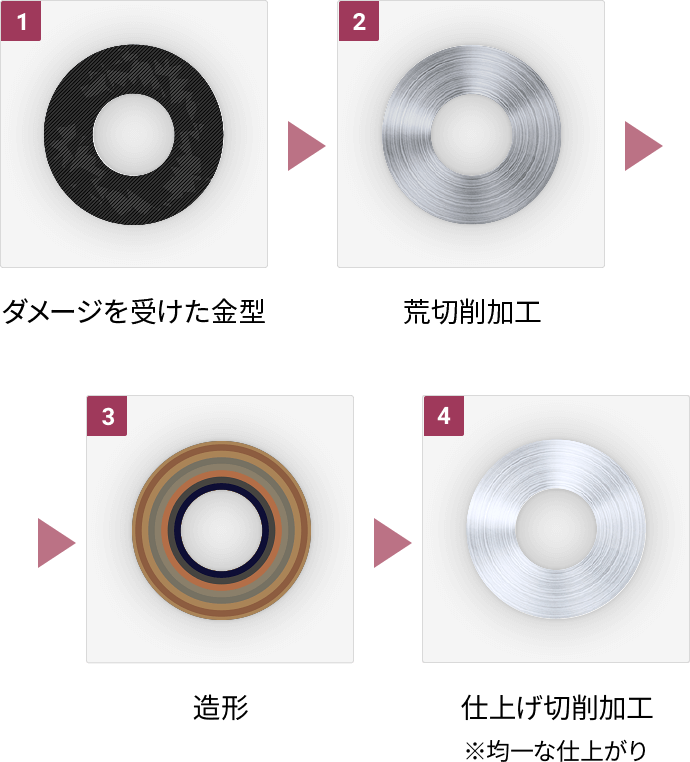
*従来 → 金属3Dプリンタにより作業時間約85%短縮
(一例における削減時間となります。TIG溶接作業員、造形内容になって異なります。)
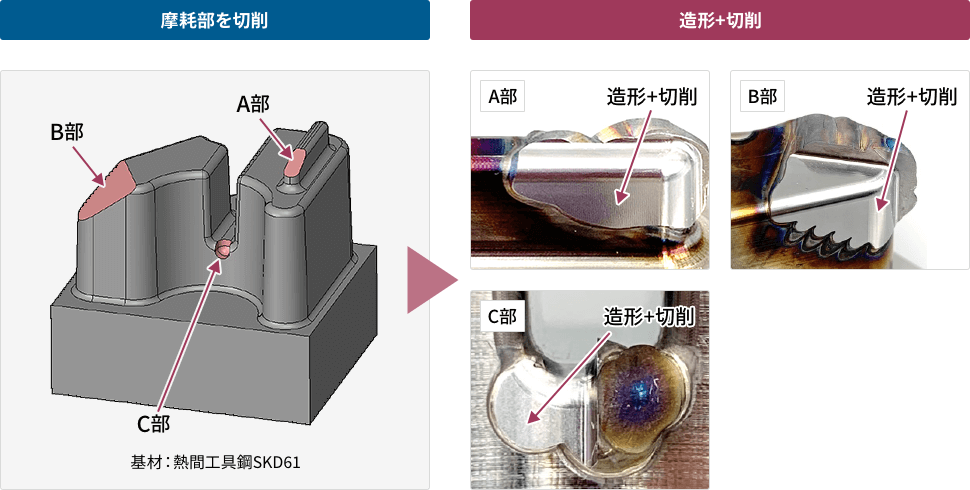
④異種金属造形(コーティング、高機能部品化)
部品、金型、工具などの強度を高めたい(衝撃を受けやすい)部分のみに、基となる部品(基材・部材)とは異なる金属材料を造形する工法です。
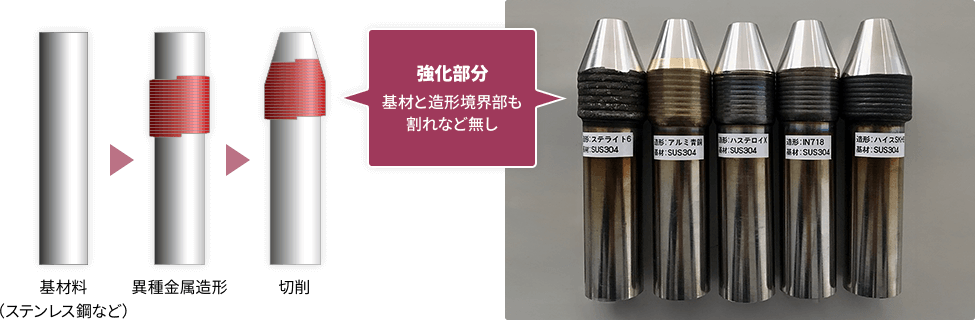
耐摩耗性向上、耐食性向上、硬度向上など部分的な高機能部品化を実現します。
ステライト (Stellite6※1) |
アルミニウム青銅 | HASTELLOY X※2 | インコネル (INCONEL 718※3) |
ハイス鋼 (SKH51) |
---|---|---|---|---|
|
|
|
|
|
- 1 StelliteはKennametal Inc. の登録商標です。
- 2 HASTELLOYはHaynes International, Inc. の登録商標です。
- 3 INCONELはSpecial Metals Corporationの登録商標です。
5.受託造形サービスのご紹介
三菱電機ではワイヤ・レーザ金属3Dプリンタによる受託造形サービスを開始しました。新たなものづくりを試してみませんか︖
受託造形サービスの流れ
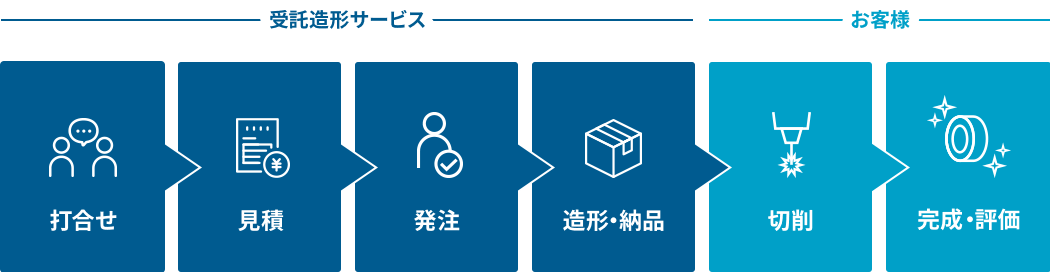
- 打合せにて、造形ご希望の形状を3DCADデータや、図面などを用いてご相談させていただきます。また、造形される側の基材(部材、部品)や、溶接用ワイヤ材料はお客様ご支給か当社手配か否かなども合わせてご相談させていただきます。
- 後加工(切削、熱処理)につきましては、原則はお客様側でのご対応をお願いしております。
- 受領可能な3DCADデータは、IGES、Parasolid、STEP、SATなどとなります。
対象材料
ステンレス鋼、熱間工具鋼(SKD61)、ハイス鋼(SKH51)、マルエージング鋼、軟鋼、HASTELLOY X※1、インコネル(INCONEL 625※2、 INCONEL 718※2 )、WASPALOY™※3、ステライト(Stellite6※4、Stellite21※4)、チタン合金(Ti-6Al-4V)、銅合金、アルミニウム合金(5000系)など
※上記に記載がない材料もお問合せください。
- 1 HASTELLOYはHaynes International, Inc. の登録商標です。
- 2 INCONELはSpecial Metals Corporationの登録商標です。
- 3 WASPALOY™はUnited Technologies Corporation (UTC)の登録商標です。
- 4 StelliteはKennametal Inc. の登録商標です。